Regional Collaboration &
New Initiatives
地域連携と新しい取組み
地域の皆さまとともに
ともに成長・さらなる発展をめざして
当社は、自動車部品の製造だけでなく、日頃の事業活動にご支援いただいている地域の皆さまへの恩返しとして、地域発展の一助となれるよう努めています。
自動車部品の製造を通じて培った技術や経験を活かし、産業の枠を超えて地域の"モノづくり"に携わる皆さまと一緒に改善活動を行っています。
【主なサポート事例】
①モノづくりサポート『モノサポ』
当社製造現場の管理経験者が、企業様へお伺いし、一緒に改善活動に取組みます。経験にもとづいた着眼点で働きやすさをご提案するとともに、改善風土の定着をご支援いたします。また、課題に合わせた専門人材の派遣で、改善を推し進めます。
②安全学習会
従業員向け安全教育施設を活用し、講義と危険体感で安全への気づきを得ていただきます。危険体感では、専用装置やVRを用いて、挟まれや落下、衝撃を擬似体感いただくことで、日常業務へお役立ていただきます。
③からくり塾・デジタル塾
日常業務の省力化に向け、弊社ではたくさんのオリジナル装置が活躍しています。からくり塾では要素技術や装置見本をご説明し、デジタル塾では体験学習でより身近に感じていただき、自社での活用についてイメージいただきます。
地域のカーボンニュートラルを目指して
地域でカーボンニュートラルを実現するためにさまざまな活動を推進しています。
①苫小牧市との共同提案が環境省の「脱炭素先行地域」に選定
産業エリアで再生可能エネルギーの拡大を図りながら、民生部門の脱炭素化を実現する計画が採択され当社では太陽光発電の余剰電力を地域へ供給する事業に取組んで参ります。
②水素社会実現に向けた取組み
スパークスグリーンエナジー&テクノロジー㈱が環境省から受託した実証事業に参加し、水素を福利厚生施設の暖房や給湯に利用する実証を行っています。
③地域の皆様への啓発活動
ゼロカーボンの取組みについての興味や理解を深めていただくため、自治体や地元企業様のイベントに積極的に参加し、トヨタの環境技術や当社の取組みを紹介する活動を実施しています。
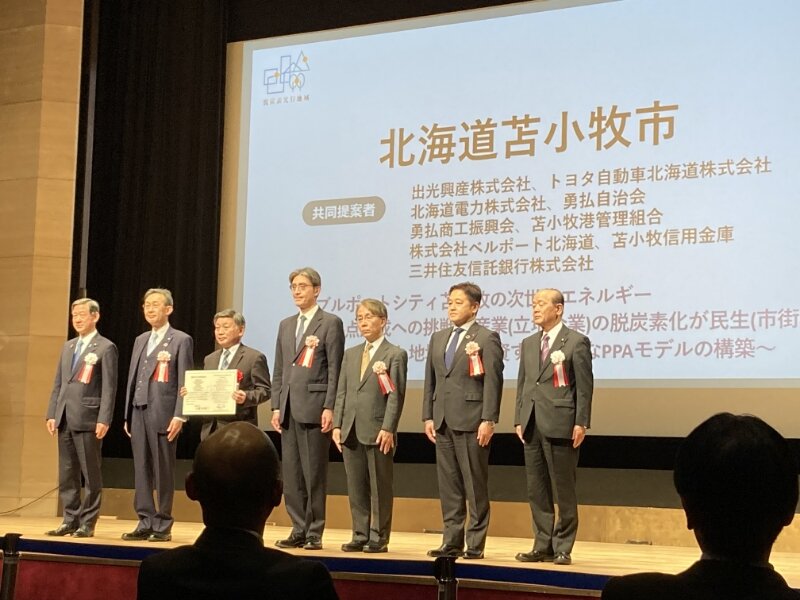
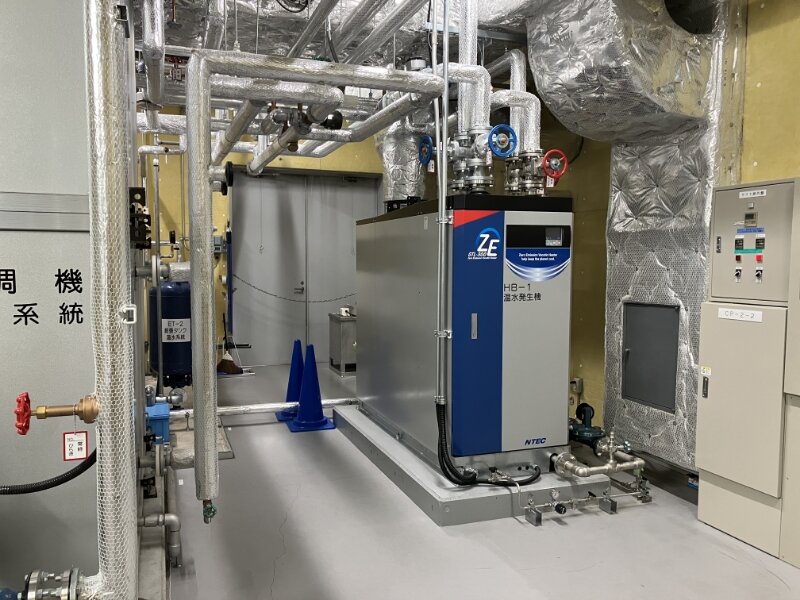
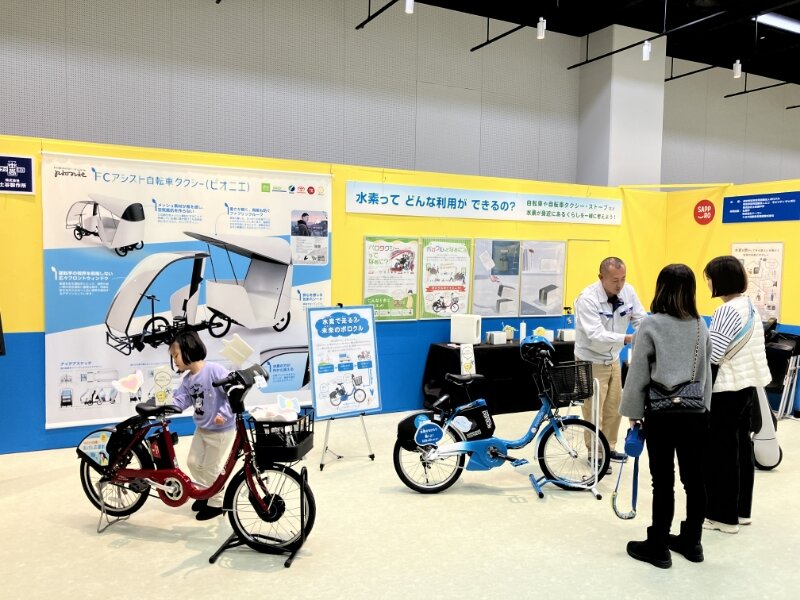
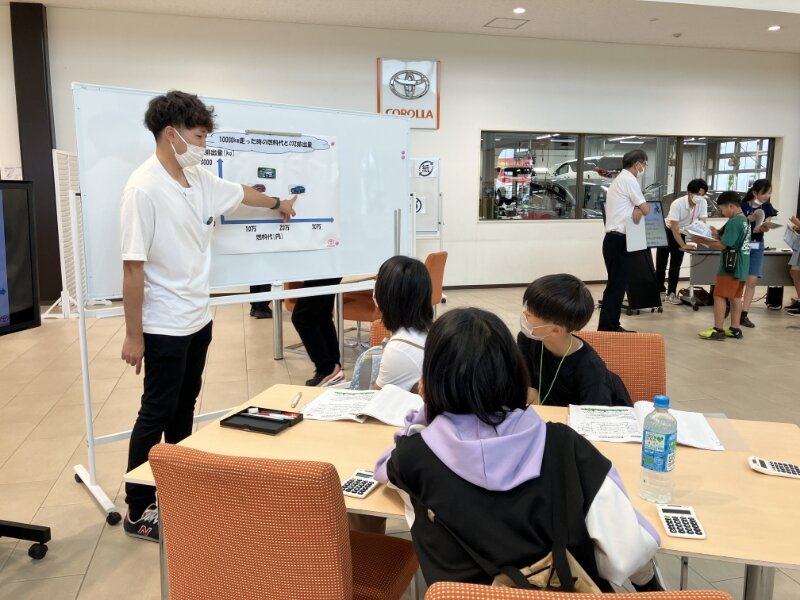
新しい取組み
ものづくりを支える技術
私たちの「ものづくり」には、品質・安全に優れ、効率の良い生産技術・製造技術を取り込んでいます。当社の技術スタッフは、これまでの知見を活かしながら、社内他部署の関係者を含め仕入先やメーカーの皆さまとともに、生産ラインの設計、新技術の導入や技術開発、既存の生産ラインにおける改善などに取り組んでいます。
【素形材工程】
①〈熱処理〉小規模真空浸炭炉×減圧焼入方法の開発
これまで当社の熱処理では、主に連続浸炭炉を使用していました。
連続浸炭炉は、同品種の大量生産を得意とする一方で、多品種少量生産は非効率でした。そのため、熱処理メーカー様にご協力いただき、小ロットでも効率的な生産を実現する特殊な手法を開発し、設備を導入しています。
※熱処理の様子は、こちらをご覧ください。☞STEP1 熱処理
②〈鍛造〉世界初 CVTシーブ 熱間ロール成形の技術開発
CVTユニットに内蔵される部品(シーブ)の素材成形において、世界初となる熱間ロール成形(逐次成形)の技術を開発・採用しています。('18年 トヨタ自動車技術開発賞 受賞)低荷重化(従来比80%減)により、設備のコンパクト化(42%減)、素材重量低減(8%減)を達成しています。
※鍛造の様子は、こちらをご覧ください。☞STEP1 鍛造
【加工工程】
〈歯車研削〉
ハイブリッドトランスアクスルを始めとしたトランスミッションには、より高いNV性能・効率・強度が求められています。重要部品であるギヤでは、その歯面を専用加工設備と砥石で磨き上げ、要求性能を満たします。
※加工の様子は、こちらをご覧ください。☞STEP2 機械加工
〈水溶性MQL加工〉
※'21年度 「省エネ大賞 省エネ事例部門 資源エネルギー長官賞(産業分野)」受賞
ハイブリッドトランスアクスルのケース・ハウジングなどのアルミダイキャスト部品の素材を加工して仕上げています。これまでの研磨や切削加工では、油性クーラントの使用や、クーラント液を常時かけ流しながら加工することが多く見られました。当社では環境への配慮と高効率生産の実現のため、油脂メーカーをはじめ関連するメーカーの皆さまとともに水溶性MQL加工を実現しました。従来に比べて、クーラントの使用量低減や切粉の堆積や飛散を防止、高効率加工による加工時間の短縮と省エネなどのカーボンニュートラルにも貢献しています。
※詳しくは、こちらの動画をご覧ください。☞省エネ大賞 資源エネルギー庁長官賞 受賞 事例発表動画
※加工の様子は、こちらをご覧ください。☞STEP2 機械加工
【組付工程】
組付は、圧入・ボルト締付などの自動設備と人の作業を組み合わせてラインを構成します。これにより月々の必要な生産量から逆算される「タクトタイム」の時間内で、安全かつ高品質、効率的なラインを構築しています。また、既存の生産ラインでは、さらに高品質で効率的な生産を目指すために技術スタッフと現場スタッフが協力しながら、日々改善に取り組んでいます。
※組付の様子は、こちらをご覧ください。☞STEP3 組付
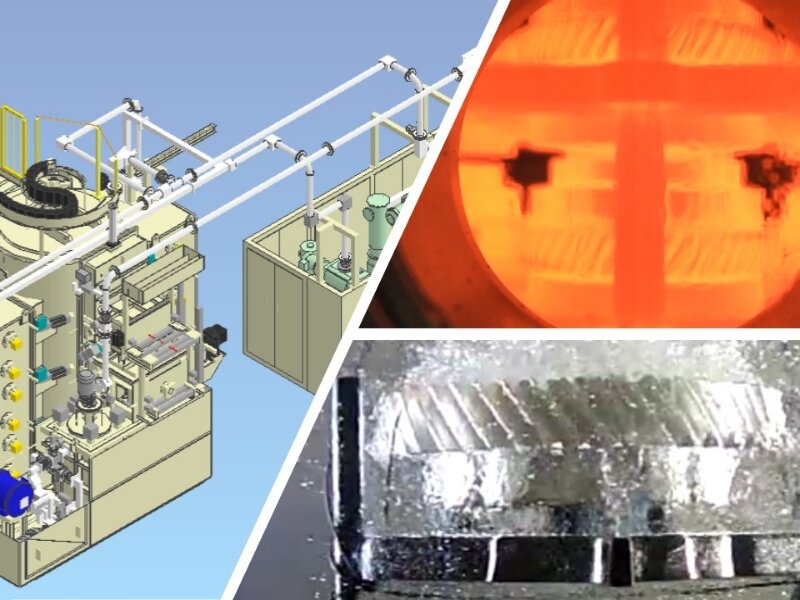
'21年度 省エネ大賞 資源エネルギー長官賞 受賞事例紹介
安心・安全をお客様のために
私たちは、毎日何百台もの駆動ユニットを生産していますが、お客様にとっては大切な一台。そのことを常に意識しながら一台一台検査を行った上でお届けしています。
【検査工程】
〈画像検査〉
組付後の最終検査として、外観の全数検査を行います。
これは、ハイブリッドトランスアクスルの外側に取付された部品が、誤品・欠品なく、正しく組付けられているかを自動で検査を行います。
約240項目をおよそ1分以内で検査します。
こちらから検査工程の様子をご覧いただけます。☞STEP4 検査
〈Assyテスター〉
ユニットの性能を保証するため、実車と同様に潤滑油を注入して検査を行います。実際の走行に近い条件で検査を行い、振動や異音などの異常が無いことを確認した上で、出荷工程に送られます。