Manufacturing
ものづくり
Step2機械加工
ダイキャスト・プレス・鍛造・熱処理工程を経た部品を切削・研磨・溶接等により、
歯車やシャフトなどの部品を正確に仕上げます。
Step3組付
機械加工ラインで仕上げた部品や部品会社から仕入れた部品を
流れ作業によって順序よく、正確に組付けて完成品にしていきます。
Step4検査
完成品の動作確認のため、
約240項目にも及ぶ厳しい検査を行います。
Step5出荷
完成した製品は、世界中のトヨタの工場へ出荷され、
車両に組み付けられます。
Previous Step
素形材工程
Interview インタビュー
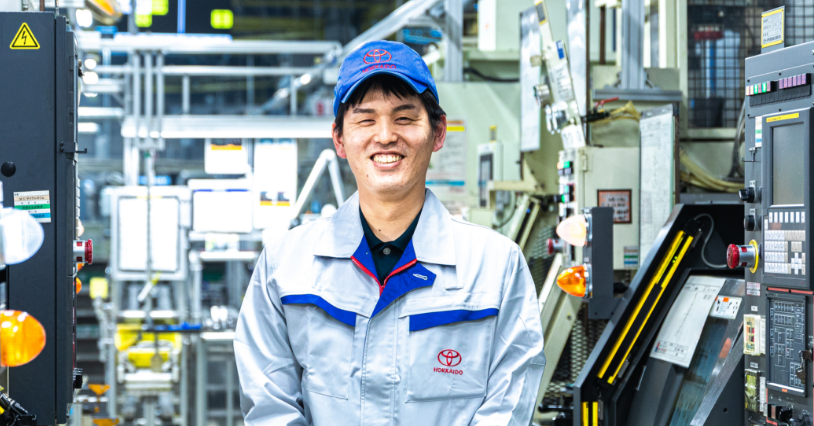
安全で効率的な作業を
常に追い求めています。
第2ユニット製造部
常本 智哉さん / Tomoya Tsunemoto
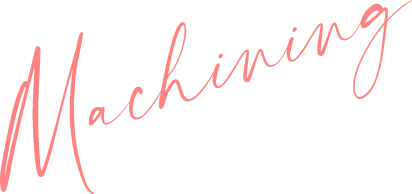
常本さんは、Drive Shift-CVTに内蔵される部品を機械で加工する工程を管理しているオペレーター。担当するラインではピストンやシリンダーなど、外注品や前工程から運ばれてきた複数の部品を機械で削り出したり、溶接して組み合わせたりして、最終的に5つの部品に仕上げています。切削や溶接などを行う機械は安全性のため内側が見えない仕様となっているので、常本さんはそれらの設定条件や圧力計などの機器の状態にズレが生じていないかを毎日チェック。不具合がある場合には原因を探り、即座に復旧できるよう努めています。「部品を機械にセットするのは作業員の役目で、彼らが仕事しやすい環境をつくるのも私の仕事」という常本さん。「トヨタ自動車北海道では毎月、作業の改善に関するアイデアを募集していて、私も必ず1つは提案するようにしています」。常本さんは以前、切削する機械の刃を効率的に当て、刃物の摩耗も減らす提案をして表彰されたことがあるといい、「表彰を目指して、これからも日々改善を追い求めていきます」
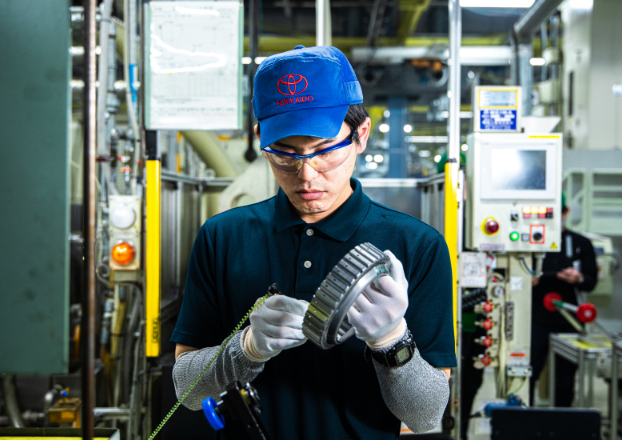
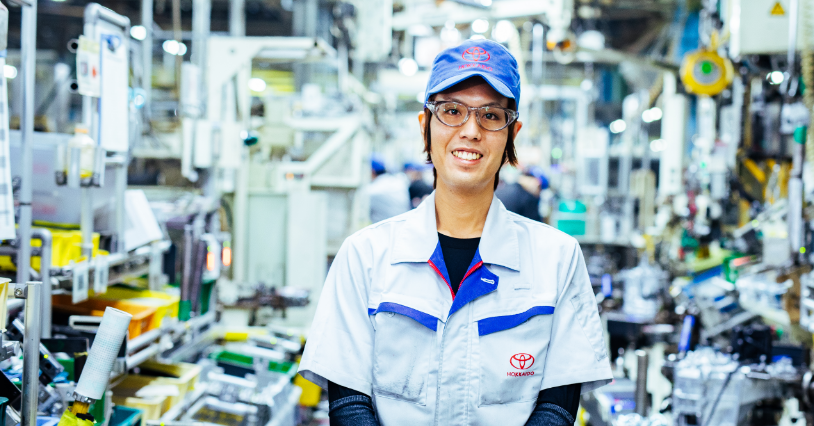
みんなで一体感をもって
丁寧に組み上げています。
第1ユニット製造部
田村 悠人さん / Yuto Tamura
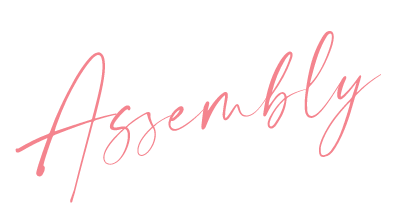
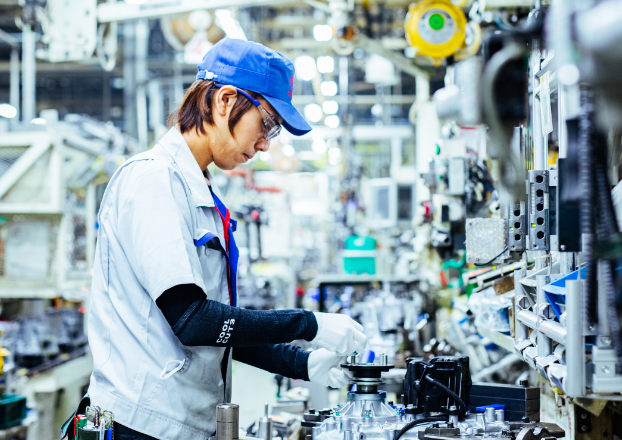
田村さんは、エンジンの力を前輪と後輪への分配や二駆と四駆を切り替える役目も果たす、トランスファーを組付する製造ラインを担当しています。 「工場内で機械加工した内製部品と、他の会社でつくられた外注部品を圧入したり、ボルトで締めたりして組み付け、製品を完成させています」。田村さんは車が好きで、高校は自動車整備科を卒業。一度は自動車整備士を目指しましたが、労働条件の良さに惹かれてトヨタ自動車北海道を選んだと振り返ります。「部品も車の一部。車体こそ無いですが、作業を通して、車をつくっている感覚を味わうことができています」。また、組立工程では、複数の人で異なるパーツを組み付けて一つの製品を完成させていくので、「一緒につくっている感覚も強いです」。そのため、「みんなの仲が良く、風通しも良い。効率の良い環境をつくることが推奨されていて、やりにくいことがあれば自分たちの提案で変えていけるので、働きがいも感じています」。